Key Design Features For Effective Processing
of Hydro Vac Slurry
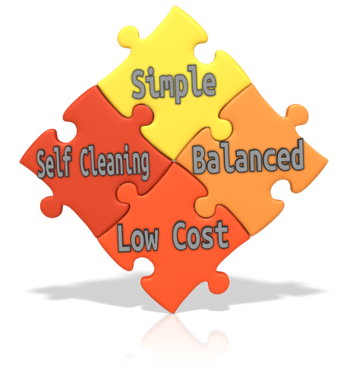
In order to effectively and consistently handle the tremendous material diversity associated with receiving and processing numerous loads of Hydro Vac Slurry in any given day, it's going to be important for a processing system to follow some very important design parameters.
We can combine all the key design elements into the following four groups or categories...
- Balanced System Dynamics. Receiving, conditioning, and processing of Hydro Vac Slurry requires dynamic management of water levels, retention, and material flow.
- Self Cleaning Equipment. Diverse material weights combined with the plastic and "sticky" characteristics of clay particles require unique holding tank design to avoid material build up on the bottom and side walls of material holding tanks.
- Simple To Operate. Ease of operations through automation minimizes head count and eliminates much of the complexity and human error that comes with staffing and controlling a manually operated system.
- Low Operating Cost. In order to maximize profitability, a Hydro Vac Slurry Processing System must be designed to minimize Labour, Power, Chemistry, and Maintenance Costs.
Balanced Vs Unbalanced System
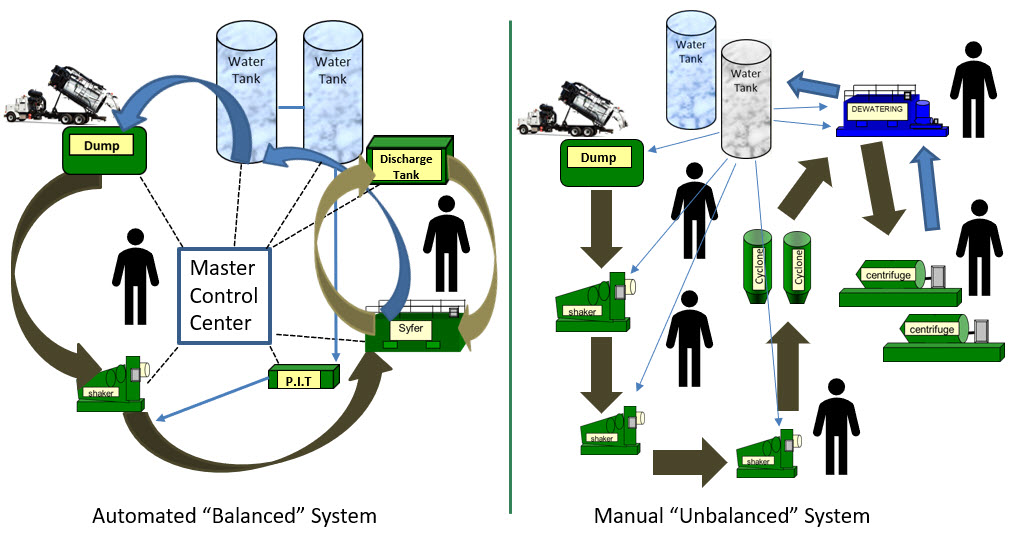
Balanced System Dynamics effectively utilize automation to orchestrate the movement of received material through the entire processing system regardless if material is received in batch lots or continuous flow.
The Master Control Center communicates with all the encoded system pumps and augers via Variable Frequency Drives (VFD's). This allows one person to operate the entire system with other support staff available to manage the processed solids discharge and any receiving administration. The operator for a balanced system does not need any type of special qualifications or operator experience, and can typically be trained to competently operate the entire system a short period of time.
An Unbalanced System is manually operated through the coordination of several individuals required to act in near perfect unison to allow this type of processing system design to work effectively. Inevitably, coordination breaks down, even if only momentarily, creating numerous potential problems including but not limited to 1) plugged pumps, 2) damaged screens, 3) overflowed tanks, 4) sediment filled tanks which individually or collectively either lead to the entire system being shut down for repair, or processed water and solids not meeting their required levels of cleanliness and dryness.
Not only is coordination difficult with an Unbalanced Manual System, but there are also special skill set requirements, particularly with respect to solids control and chemistry management.
Self Cleaning Equipment
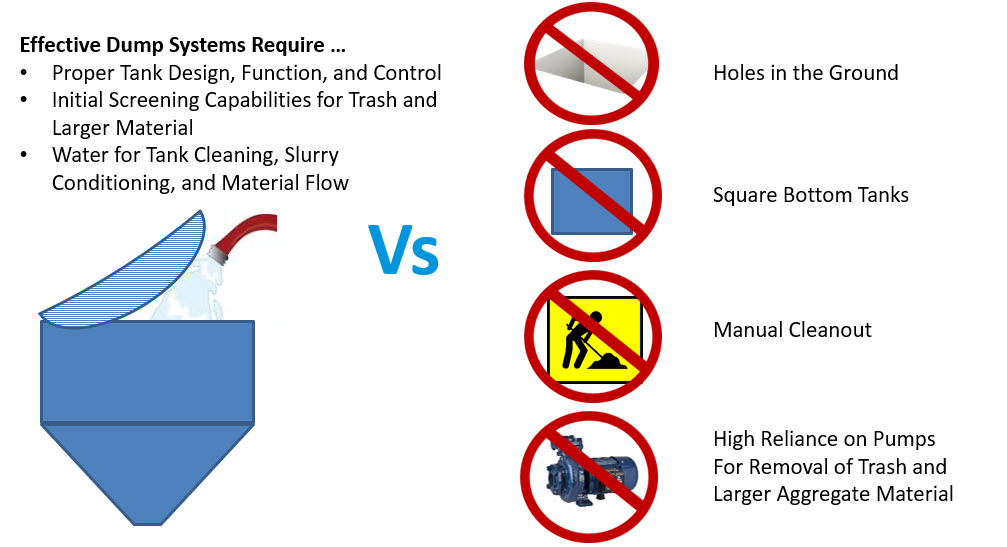
In order for any mechanical processing system to be effective receiving and processing Hydro Vac Slurry, the entire processing line must be designed to properly handle the material flow with minimal human intervention.
To accomplish this, all material holding compartments and tanks need to have screening systems, wall designs, floor designs, and wash out systems that eliminate the build up of sediment from material flow.
Aggregate and soil settling can only be allowed to take place where it aids the process without plugging up the entire material flow regime.
Simple To Operate
With respect to Hydro Vac Slurry Processing, a proper definition for "Simple To Operate" would include an easy to learn and operate control system for a processing plant that has limited down time and consistently produces the desired results which include cleaned water and dried solids for re-use or disposal. The best way to achieve "Simple Operating Status" is through the combination of the following three elements ...
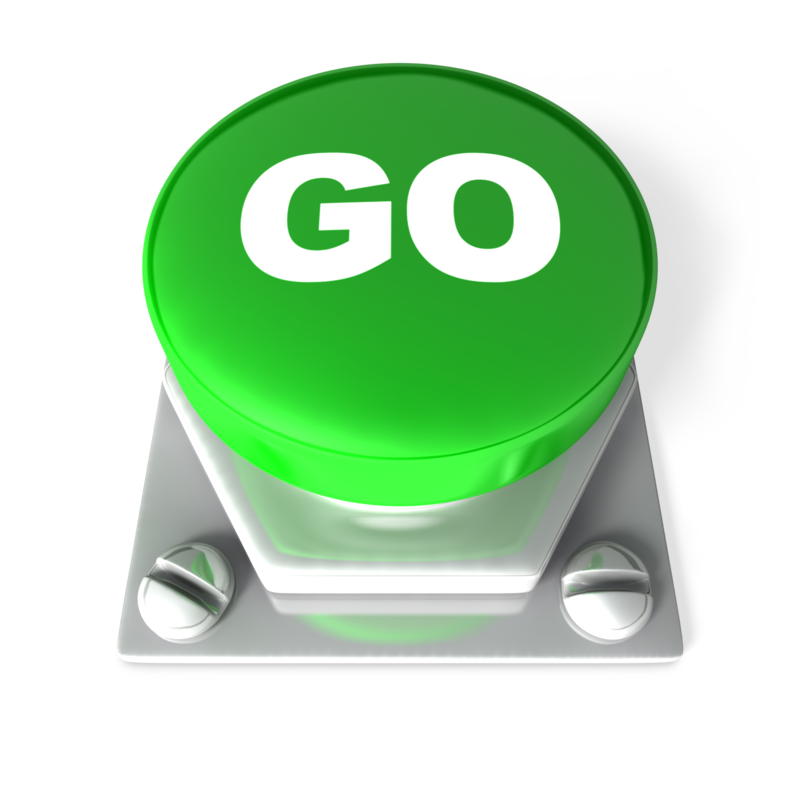
Automation
As mentioned above, total system automation allows a single operator to be in full control of the entire processing system. Automation controls should allow the operator to spend the majority of time observing plant operations and monitoring the generated outputs to make sure the desired results are consistently being achieved.
System operation should be low stress and the control system should have built in operating parameters to guide the operator as well as safeguards to minimize operator error.
24/7 Remote Operational Ability
This refers to an operating standard from many other industries that require dewatering processing systems to operate on a 24 hour a day, 7 day a week basis.Hydro Vac Slurry Processing does not require anything close to 24/7 capabilities. Most of these processing plants will likely operate less than 12 hours a day for 5 to 6 days a week.
But what Hydrovac Slurry Processing does require is a highly reliable system ... one that can deal with varying loads, the stop and start issues related to batch processing, and the daily processing volume requirements.
The best way to build a highly reliable, high capacity, low maintenance processing system, is to overbuilt it ... design it for 24/7 remote operations where high up time and low maintenance are both critical to ongoing operations.
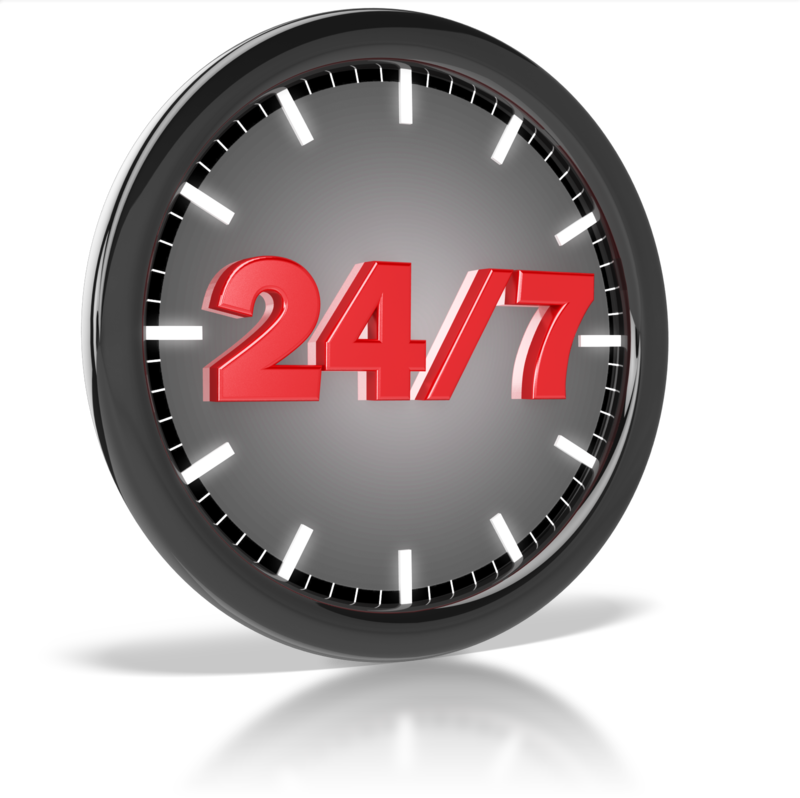
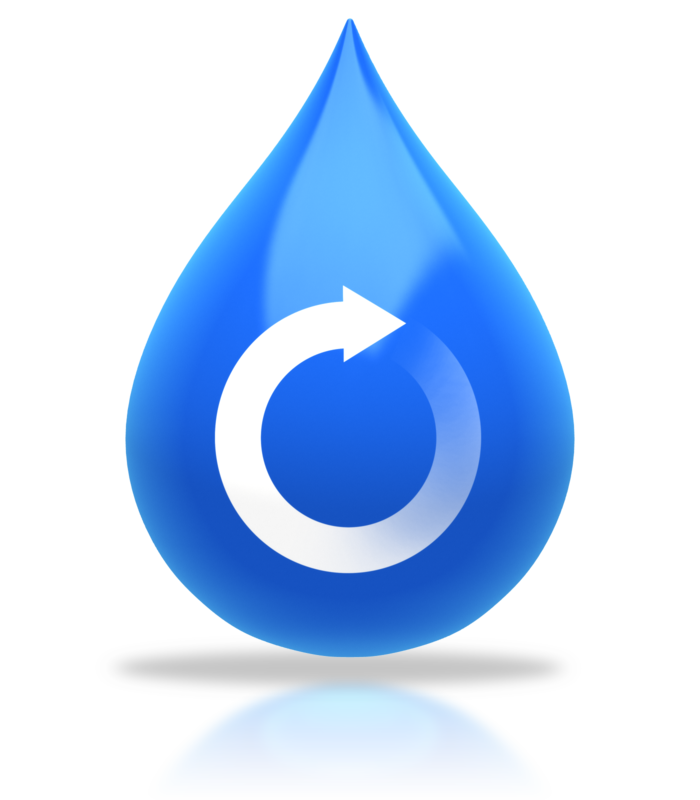
Clarification Technology
The simplest, easiest, lowest cost way to clean water and dry solids is through the use of Clarification Technology.
That's why its widely used in industries such as 1) Sewage Treatment, 2) Food Processing, 3) Rendering, 4) Mining, 5) Construction, and 6) Oil & Gas.
For Hydro Vac Slurry Processing, the key is finding small scale Clarification Equipment with the necessary processing capacity.
Low Operating Costs
As with any processing system in any industry, consistently low cost operations are going to be important to success. For the Spectur Hydro Vac Slurry Processing Systems, the Operating Cost Dynamics are as follows...
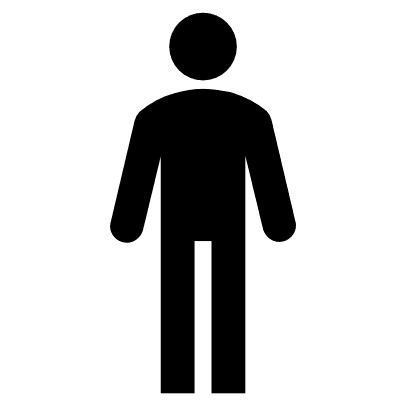
Labour Cost
Spectur's semi automated balanced system allows one operator to be in complete control of plant operations. This is not only critical for optimal plant performance, but also for management of total labour cost. One primary operator, will tend to work with two or three support personnel for on the ground maintenance and any administration requirements in the receiving process. So if you have total operating head count of 3 or 4, you likely have a labour pool of 8 to 10 to manage, depending on your total weekly operating hours, shifts, etc.
For manually unbalanced systems, the labour requirements can be 5 to 7 people for similar processing capacity. Therefore, you're trained and available labour pool will be likely need to 15 to 21 in total with a lot of specialists and cross training requirements.
Hourly labour cost is one thing, but when you factor in all the training, HR, turnover, severance, etc., total labour cost can quickly eat up a significant portion of earned revenues.
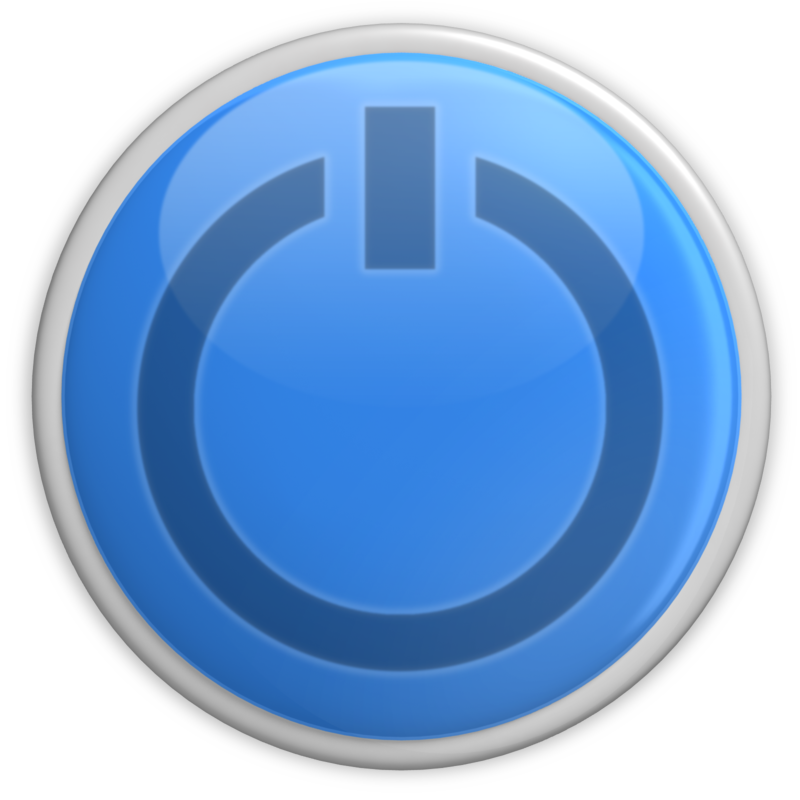
Power
All Spectur Hydro Vac Slurry Processing Plants operate on 3 Phase, 480 Volt, 600 Amp Electrical Power.
The base configuration operates on 225 HP.
All pumps and augers are over sized and will typically run at 75% of their maximum power specs.

Chemistry
Spectur's system is designed to use the least amount of chemistry possible to help achieve effective agglomeration of the fine colloidal solids that are suspected in the water.
Hard water is required for the flocculation process, so if you're adding hard water from a local source, no hardening agent would be required. In most situations, an Organic Coagulant is added to a minimum concentration in water.
Spectur also adds a very small amount of biodegradable polymer that mixes with the coagulant and suspended solids to form the larger particles required for fine solids removal from the water .
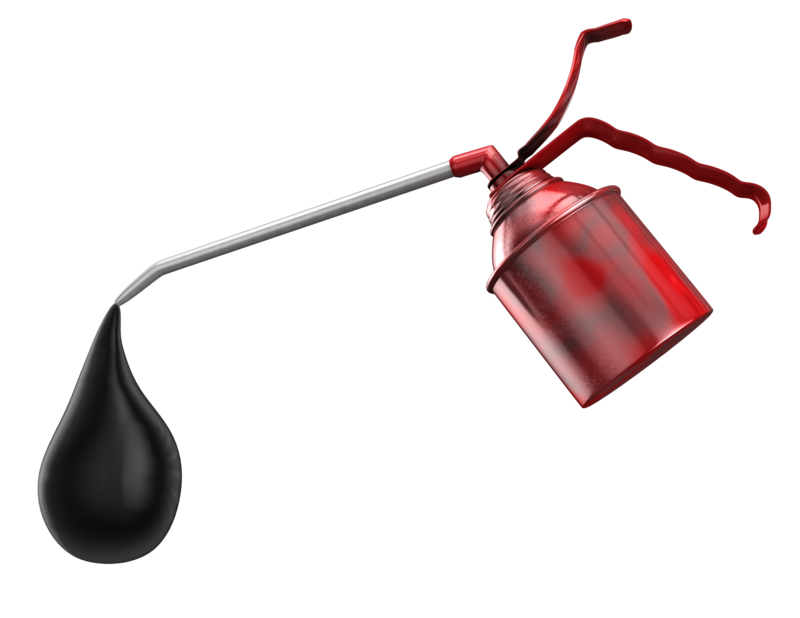
Maintenance
As mentioned earlier, the entire processing system is designed for remote 24/7 operation. All pumps and augers are over sized in order to run well below the required capacity. The same pumps are utilized through out the system. The augers have 1/2 inch custom made fighting and are supported by hanger bearings.
The daily maintenance involve greasing machinery through out the plant. The only high wear part is the impeller in the solids pump which may have to be replaced every 6 to 9 months. Replacement can typically be done on site by plant workers within a in few hour.
Estimated Weekly maintenance costs are estimated to be between $500 and $750.
To find out more, click here to send us an email with any questions you may have.